With the front triangle done and the dropouts in the chainstays, it's time to attach the rear triangle. I usually jig up the whole back end at one time, then tack it all. Chainstays to BB first, then seatstays to seatlug and seatstays to dropouts. The chainstays are very straightforward, seatstays take a little more time to jig up correctly. For this frame the customer wanted them

Here's how they looked mitered up. Sorry about the bad picture, it was taken with my phone, couldn't find the camera that day.
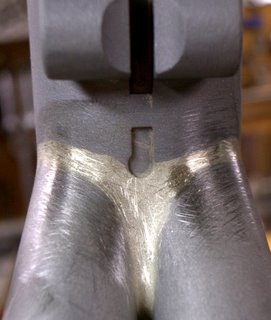
Here's how it looks after removing the flux and hitting it with some 80 grit. There's virtually no way to file or sand between the stays, so you have to make sure you lay that silver in there perfectly with the torch. I kept the fillet as small as possible as I didn't want a large amount of silver showing around the seatlug (remember, no paint).
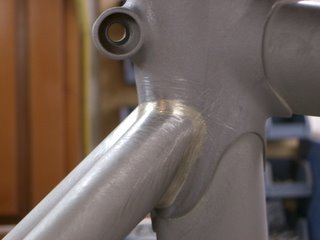
As you can see, I keep a uniform sized fillet all the way around the stays. That's not easy to do, but again, since there's no paint to hide anything I want it
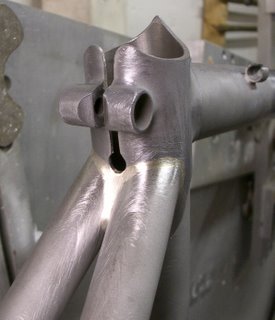
And finally, here is how it looks after finishing up the seat-post clamping slot and cleaning up the seatlug.
One challenge that came up on a frame this size with compact geometry and 19mm seatstays is the length of the brake bridge. The rear end is very tight on this frame, 40.5cm chainstays and a sloping top-tube means the seatstays are quite short. When combined with the fastback attachment that makes a very tight area for the brake bridge.
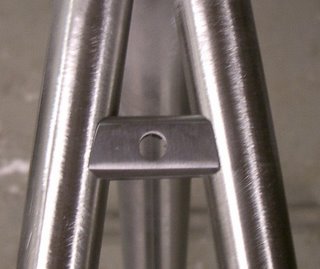
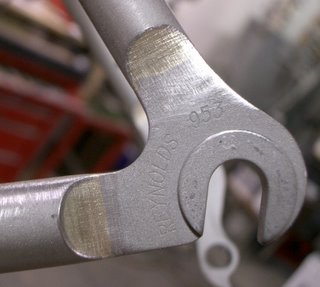
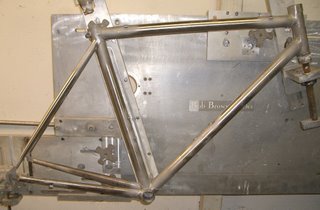
Finally here's the fully built frame. I won't say it's finished because I still need to put the final finish on the stainless, but all brazing and filing are done. I'll have some pictures of the frame with the final finish in the next episode.
In other news....
I took yesterday afternoon off work, it was what will probably be the last really nice day of the fall. About 65 degrees and sunny with a forecast of 30 and windy the rest of the week. It was a moral imperative to go for a bike ride. So I broke out the fancy road bike and headed to Afton. Spectacular day for riding, wearing shorts and short sleeves felt great. I wish my legs felt as good, but they made it though and I felt really good at the end. Today it's 35 degrees out and windy as hell, glad I rode yesterday.
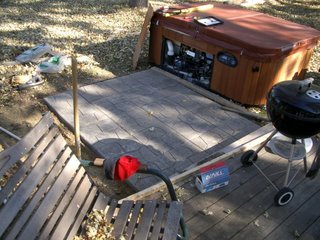
Yup, got a hot-tub. Never really thought I would, but the price was right, free. A huge thanks to my Sister-in-law's Dad who gave it to us. I had to put down a suitable pad to mount it on and I'll have to expand the deck slightly to give us a walkway. The pad went quickly but wiring it up has proven to be a challenge.
The thing has the craziest wiring I've seen. It comes stock set-up for 120v service, 20 amps. That's simple to hook-up, but it also limits the heater output and it can only run the pump or the heater, not both at the same time. So in an outdoor application the water would cool off pretty quick (especially in MN in the winter). So I followed the manufactures wiring diagram to convert it to 230v service. Well, they require a new bub-panel be installed in the vicinity of the tub, and that you have 2 GFCI breakers in that sub-panel, one of which is 120v, one is 240v. Very odd. To make it worse apparently every other hot-tub on earth just uses a single 50amp GFCI breaker in this sub-panel because they sell kits to accommodate that all over the place for pretty cheap. But the internal wiring in this baby is set up as two discrete circuits, a 20amp 120v and a 30amp 240v. None of the internal wiring is large enough to handle 50amps, so You're really stuck using this goofy set-up.
Of course no home-improvement type place actually stocks the required breakers to make this happen (you need a 30amp, 3 pole GFCI breaker!). So after calling every specialty electrical supply place in town I finally found 2. One was $168, the other $120. I opted for the $120 since they were identical part #'s. So hopefully tonight I'll be able to finish this up and start heating some water.
So between the $160 worth of wire needed to run the sub panel, the breakers, box, concrete pads,filters, etc... This "free" project is up to about $500. Oh well, it's still a great deal since the tub would have cost 10x that alone and most importantly it will make Beth really happy (and me too!).
bbbb
1 comment:
You sly dawg you!
A hot tub eh?? Makes me think Will Ferrell as the Professor in those SNL skits practicing the ancient art of Shin-Shi Shin-Shi.
[gag]
;-)
-Me
Post a Comment