Anyways... The best part about doing repaints is getting to see naked frames! Seriously, I love seeing how other builders or companies do things and you can't tell that through layers of paint and putty. I've got a unique batch of frames in right which include an Original Tom Ritchey fillet brazed bike, an 80's Pinnarello, a 70's Falcon, and a few other regionally made handbuilts by several builders who shall remain nameless. They really represent a variety of construction methods and quality levels.
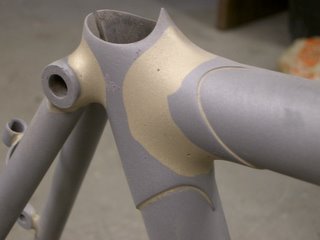
The Ritchey 1s probably my favorite in terms of the sheer amount of time Tom must have put in to this thing. It's a unique design that Tom used with "pseudo-lugs" at the head-tube and seat-tube. He made tubing sleeves to slip over the tube, then layed down huge fillets over those to make the appearance of lugs, but they're not exactly lugs. The seatlug shown here is the closest thing to a lug as it had sleeves on both tubes. The finish work on the fillets is amazing, they're huge and flowing and hardly a pinhole anywhere. The shape is great (if you like huge fillets) and very even.

The headtube is pretty neat too. With paint on it, this looked pretty close to being lugged, but in reality, the bands on the ends of the headtube were machined in place. Yup, he turned down the headtube from a thicker tube just to get those reinforcing bands on the ends. Again, the huge fillets give a very unique look to the joints, and the "lug" points are filed very thin and even. Very clan brazing on them as well, especially for using brass. To be honest, these are the best shaped (in terms of not needing any filler to look like a perfect radius) that I've seen on any bare frame.

The brake bosses are impressive as well. No need to worry about those suckers coming off! this is the largest build up of brass I've seen on a boss, but he sculpted it very well. This is purly an artisan touch, no functional value at all. Probably not something I would do as I don't like the look, but the execution is fantastic.
Overall, nice work Tom.
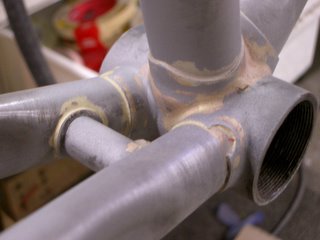
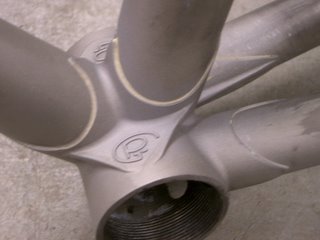
This next one is a mid 80's Pinarello. I've done a few Pinnarello repaints and I have to say I'm consistently impressed with the quality on these. Most Italian frames of this era were constructed similarly to the Falcon shown above; overheated and sloppy. Pinnarello seemed to actually care about build quality though and really hit the details. This frame was actually silver brazed which is quite unusual due to the higher cost of silver. The lugs, shell, crown and dropouts were all investment cast specifically for Pinnarello (which is a huge investment). All the cast part shave detail engravings, and all the brazing is
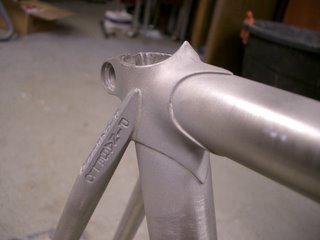
Honestly these are the only Italian made frames I've come across that really impress me. Most of them historically have been pretty shoddy.
I keep thinking more and more about my painting business and if it's worthwhile. These repaints are really kind of a time-sink. I raised my prices pretty significantly last year and it cut out a certain portion of the business, but not as much as I figured it would. The paint supply market keep changing too, which only makes things harder. My local paint supplier used to have 3 locations, one of which was within walking distance. Now they're down to 1 location and it's about a 15 minute drive for me each way. I'm sure the reason for this is the raw material costs keep going up causing them to have fewer over-the-counter type of customers (the small guys like me). VOC requirements keep getting tighter, which I'm in favor of, but it makes the product more expensive.
Lately I've been having decal issues too. More and more people seem to want restoration style finishes, meaning they want exact replacement decals. Often I can get them, but it takes weeks and they have to be shipped from Europe, otherwise I have to recreate them and have them made locally. I've got a fantastic decal guy here in town, but he recently moved to the complete other side of town, so if I need to work in person with him to fine tune colors or patterns, that's an hour's drive each time.
I figure as an average, I spend about 1 hour of my time just driving to get materials per paint job. When you have 5 to do in one week, that's a ton of time that could be spent building frames. I still do make money painting, and the paint service brings customers to me that otherwise would have never heard of me, but it also take a big chunk of my shop time away from building frames. That adds lead time to every order and probably costs me some orders for that reason, so there are trade-off both ways. Maybe I'll just raise my prices again and see what that does, otherwise I may even consider not doing re-paints at all (just painting my own work).
well, enough whining, I gotta run.
bbbb
No comments:
Post a Comment