Labor day weekend, the name says it all. This weekend's mission was to build a new shed in our back yard. I had reinforcements, well one anyways. Beth's parents came to town along with another couple who are friends of the family. So while all of them went out shopping, Beth's Dad (Bob) and I worked.
I had a pretty good plan layed out or so I thought. We wanted to put the shed next to the house, in a narrow strip of land that's pretty much useless. Unfortunately with all the Phone line work Qwest has been doing in our yard, they added an above ground junction box back there and dug in new lines through the area I wanted to use. Then I found out one of the neighbors still doesn't have working phone service off that line, so it's a sure thing Qwest will be back showing us their spirit of service by digging up our backyard again.
Therefore we decided to relocate the shed rather than have to move it when Qwest decides they messed up again. We moved it to the Northeast corner of our lot, tucked back in the trees. It's actually a great spot for a shed, fairly out of the way, and it blocks out some ugly parts of the neighboring yard. Downside is that it's on a hill, a short but steeply sloped hill which required some digging. So before we even started we were behind schedule since we now had to dig out a big chunk of earth.
Thankfully Pat (my contractor that did the addition) was working next door that day and he had his Bobcat there. It didn't take much to convince him to bring it in the back yard and do the digging for us. That alone saved us about 6 hours of digging through tree-roots trying to level the ground. What a guy.
Once he had worked his magic, we assessed the situation and decided we needed some kind of retaining wall to hold back the slope now. Fortunately it would be completely behind the shed, so it didn't need to be anything fancy, a few left over 2x8's and a couple posts worked fine. The first day we got the ground all leveled, placed and leveled the concrete blocks that would support the structure and built the entire base-frame of the shed. We wrapped that up by about 3pm and headed off to Menards to purchase the lumber we'd need to frame up the walls and roof the next day. That turned into it's own adventure.
We took my car (jetta wagon) with my trailer, same as I'd done about a hundred times throughout this project. Got to the store fine, and made our order at the lumber desk. Now, I had been having an intermittent issue with the clutch on the car about a month ago. Somehow the Hydraulic clutch had gotten some air in the line and wasn't releasing fully, making it exceedingly difficult to shift. I bled the clutch and the problem was fixed, or so I thought.
The car wasn't shifting very smooth on the way to the store, which has me mildly concerned, but not worried. But when I pulled it into the lumber yard to load up, it wouldn't shift at all. I could shift it fine with the engine off, but as soon as I started it, I was locked in a gear and the clutch wasn't releasing much at all, so stopping didn't work so well either. We continued loading lumber since it was all paid for and I figured I could get home. We had about 1000 lbs of wood on the trailer I'd guess and I came to the rationalization that I was going to have to drive home in second gear and not stop.
So we took back streets home, with flashers on the whole way. I could get the car to shift from 1st to 2nd with a bit of coaxing, but it was more like a powershift, which doesn't actually work well with this transmission. I'm not sure how Volkswagen designs their transmission, but there's no grinding or clunking when trying to force a shift, you simply can't move the shifter into position. period. Clever in that you don't tear up the syncros, but virtually impossible to shift if the clutch goes out, unless you have divine intervention to line up the gears just right as you're trying to jam the lever around. less than ideal.
So I left it in 2nd gear all the way home. I avoided stopping at all costs since I had to turn off the engine to actually come to a complete stop since I couldn't get the clutch to release much at all anymore. But eventually we made it home.
The next day we started off by bleeding the clutch again, I figured that would fix it for another week or so until I could figure out where the leak is. No dice. No amount of bleeding will get this thing to release. But during the process I could see a small amount of fluid coming from the slave cylinder bleed screw area. Got the car down to the garage and left it there, too much shed work to do, the car would have to wait.
We framed up all the walls pretty quick, then got going on the trusses. Once we figured out the angles for all the cuts, those went up quickly too. After that, we started on the siding, which really started making it look like a shed. We got about 80% of the siding up and were beat, so it was time to call it a night and get some dinner.
Sunday, Beth's Folks decided to leave town early to avoid traffic, so they were up at 5:30 to hit the road. We saw them off and promptly went back to sleep. I was still beat. Once I got up at 9, I headed out to see what I could get done. Unfortunately it was wet and the forecast was for more rain. I managed to get the last 2 sheets of siding up, but that was about it. The rain came and didn't let up all day and night.
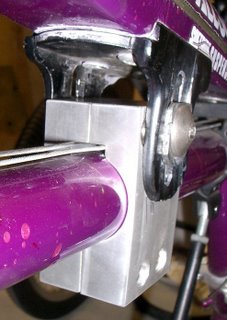
I headed to the shop to finish up some indoor work that I had wanted to get done. I machined a neat little fix for a custom trike with a softride beam. The bike had the old clamp-on beam mount and the rider had crashed and broken the mount. Softride hasn't sold these for years, so I had to come up with a more robust fix. I debated brazing the right fixture on the frame, but that would damage the paint and still require me to make the fixture, so instead I machined out a new beefier clamp-on mount. This one should hold up for years!
It was kind of fun to make too, a nice machining project. Not to mention it'll get the owner back out on the road quickly, which was my main
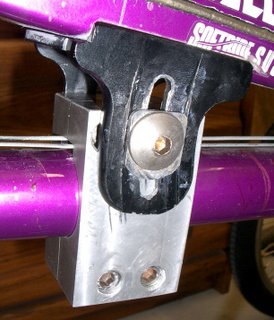
concern since this trike belongs to a woman with Muscular dystrophy and this is really her main transportation. It's a neat bike, upright trick with the beam, with a special mount out front specifically designed to hold a milk-crate nice and low where it's easy to load. I haven't heard of the maker before, the only decals say "Rain City" and it was supposedly custom made for this woman. Anyone heard of it?
Monday the skies cleared and I headed back outside to work on the shed again. I managed to get all the roofing up. That ended up taking far longer that I thought, but that wasn't due to the roofing, but rather the crappy 2x2 boards I had used to fasten the roofing to. I tried this new stuff called Endura roofing. It's a corrugated asphalt product that comes in 48" x 79" sheets.
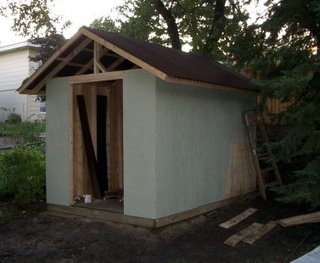
You simply need 18" spaced purlins to nail it to, no plywood to shingles required. I thought it would be a big time saver to install and it would have if I had made the purlins a bit more stout. As I was I ended up fixing or replacing about 1/3 of the purlins as I nailed roofing on. Frustrating, but in the end, It's all up and it feels pretty darn secure. I think it looks pretty good too.
The green on the siding is just primer, not finished color. Eventually it will match the house, which is a much darker green. Hopefully between the green paint and brown roof it will blend in pretty well with the trees.
I've still got to finish the siding on the peaks, build the doors, put up the trim and install the window. It sounds like a lot, but I think it should take one more solid day then it should be ready for final paint.
Now I have to go figure out what to do with my car....
bbbb